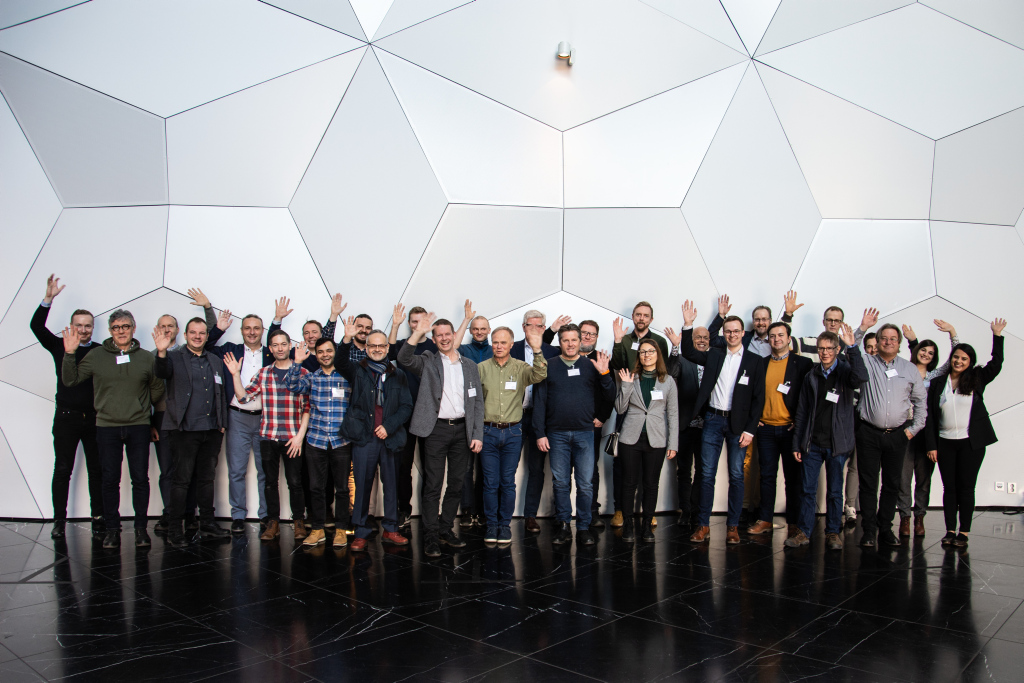
HydroFlex Workshop 23 March 2022. Clarion Hotel i Trondheim. Foto: Maren Agdestein/NTNU
Introduction
The fourth HydroFlex workshop took place on March 23, 2022. The workshop took place in Trondheim, Norway and was arranged by NTNU.
The overall question raised in the workshop was:
The role of flexible hydropower in the future energy system?
The HydroFlex project is 4 years, 5.4 mil € research project financed through EUs Horizon 2020 program. The aim of the project is to increase the value of hydro power through increased Flexibility. In this public workshop, organized in conjunction to the last plenary meeting of the project, some of the key results from the project will be presented.
• How flexible can a Francis turbine be operated?
• How to increase flexibility of the generator?
• Can we analyse and understand the trade-off between increased flexibility and environmental impact?
• And what is the public acceptance for more flexible operation?
After a winter with unprecedented price peaks and high volatility, the question of the role of highly flexible hydropower is more pertinent than ever.
The program of the workshop is listed below.
Time Title Presenter 09:00 Welcome physical and digital participants Ole Gunnar Dahlhaug 09:15 Presentation of HydroFlex project Ole Gunnar Dahlhaug (NTNU) 09:25 Hydropower in the European energy system: Future flexibility requirements (WP2) Peter Wirtz (RWTH Aachen University) 10:30 Increasing Flexibility of Francis Turbines (WP3) Igor Iliev (SINTEF) 11:00 Converter controlled synchronous machines, overcoming challenges in generators to switches (WP4) Urban Lundin (Uppsala University) 11:40 Mitigation of environmental impact from flexible hydropower (WP5) Staffan Lundström (Luleå University of Technology) 12:10 To flex or not to flex? – that is the question (WP6) Multiconsult 12:35 Panel discussion 13:50 Closing remarks from Project Officer Sebastien Mortier 14:00 Closing remarks from Project Coordinator Ole Gunnar Dahlhaug 14:10 End of program
Time | Title | Presenter |
09:00 | Welcome physical and digital participants | Ole Gunnar Dahlhaug |
09:15 | Presentation of HydroFlex project | Ole Gunnar Dahlhaug (NTNU) |
09:25 | Hydropower in the European energy system: Future flexibility requirements (WP2) | Peter Wirtz (RWTH Aachen University) |
10:30 | Increasing Flexibility of Francis Turbines (WP3) | Igor Iliev (SINTEF) |
11:00 | Converter controlled synchronous machines, overcoming challenges in generators to switches (WP4) | Urban Lundin (Uppsala University) |
11:40 | Mitigation of environmental impact from flexible hydropower (WP5) | Staffan Lundström (Luleå University of Technology) |
12:10 | To flex or not to flex? – that is the question (WP6) | Multiconsult |
12:35 | Panel discussion | |
13:50 | Closing remarks from Project Officer | Sebastien Mortier |
14:00 | Closing remarks from Project Coordinator | Ole Gunnar Dahlhaug |
14:10 | End of program |
Review of content
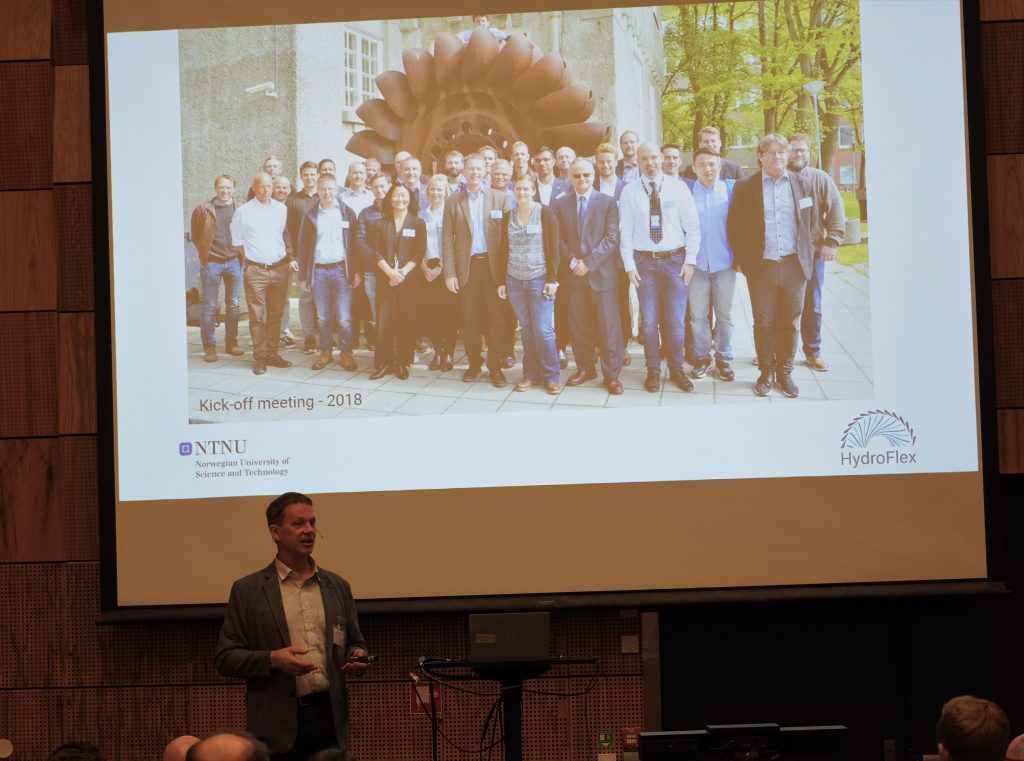
Ole Gunnar Dahlhaug , NTNU. Photo: Nirmal Acharya
In the following a summary of the talks during the workshop, highlighting the most salient discussions and conclusions.
In his opening of the workshop, the coordinator for the Horizon 2020 project HydroFlex, Professor Ole Gunnar Dahlhaug, NTNU summarized the overall challenges that the project is addressing: “Developing hydro turbine technology that permits 30 start-stops and faster ramping rates”. Based on the market simulations from RWTH Aachen, it is not likely that this radical change of operation will be observed in the Nordic hydropower plants. However, this, possibly stretched goal has been an impetus to research new technology both for turbines and generators as well as environmental impact and social acceptance.
Video from workshop_Introduction_Ole Gunnar Dahlhaug
Hydropower in the European energy system: Future flexibility requirements (WP2)
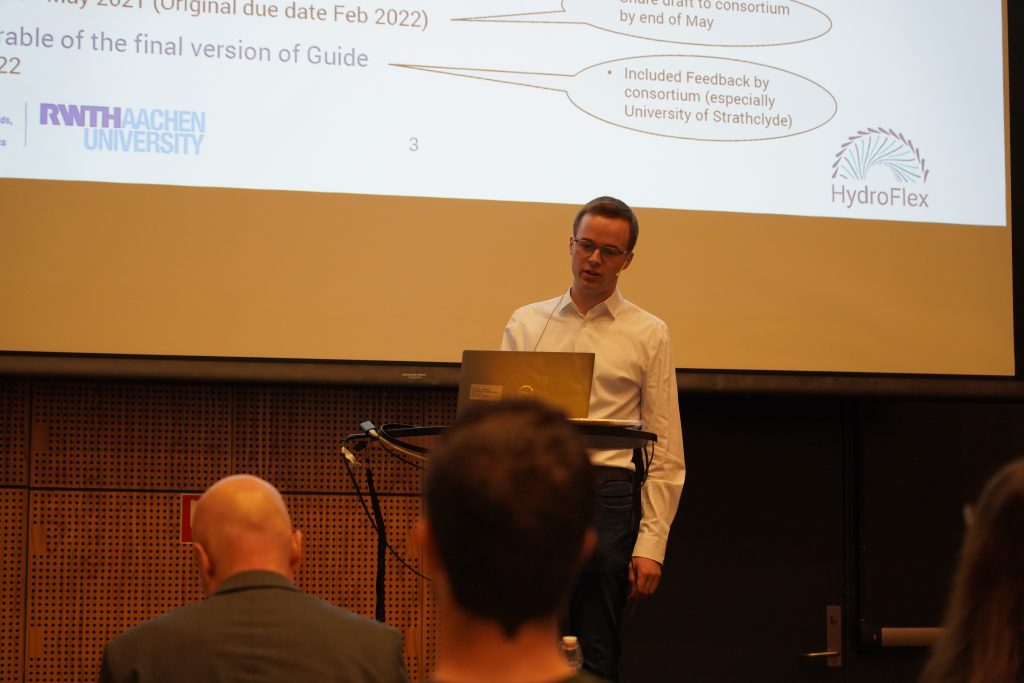
Peter Wirtz, RWTH Aachen University. Photo: Nirmal Acharya
PhD-student Peter Wirtz summarized the results from work package 2. The team from the University in Aachen have developed two simulation models to evaluate and predict the future need for flexibility in the Nordic power system. The market simulation model combines both the Continental European synchronous grid (UCTE) and the Nordic synchronous grid. As part of the work a heuristic hydraulic unit commitment model has been developed. Due to the large number of powerplants, the model was aggregated to keep the solution time manageable. However, the reference sites were kept as separate units to investigate the impact on the flexibility requirements. As a basis, three different scenarios for the future energy mix and consumption were evaluated. To further investigate the sensitivity of the model an additional fourth scenario with additional wind power development in the Nordic region was added afterwards. The main conclusions from the market simulations were:
• Day-ahead/intraday simulations show only moderate increase in flexible operation (e.g. start/stop) in the reference plants
• The change in flexible operation is strongly correlated with development of variable renewable energy in the Nordic
• The interconnections (e.g. cables) is mainly involved in energy transfer and play little role in the development of flexibility requirements
The second model is performing dynamic time domain simulations focusing on frequency stability. The question addressed is how the Nordic system will behave in a future energy mix where all nuclear power plants are substituted by wind power. The conclusion is that hydropower plants are essential to maintain frequency stability in a future energy mix.
Increasing Flexibility of Francis Turbines (WP3)
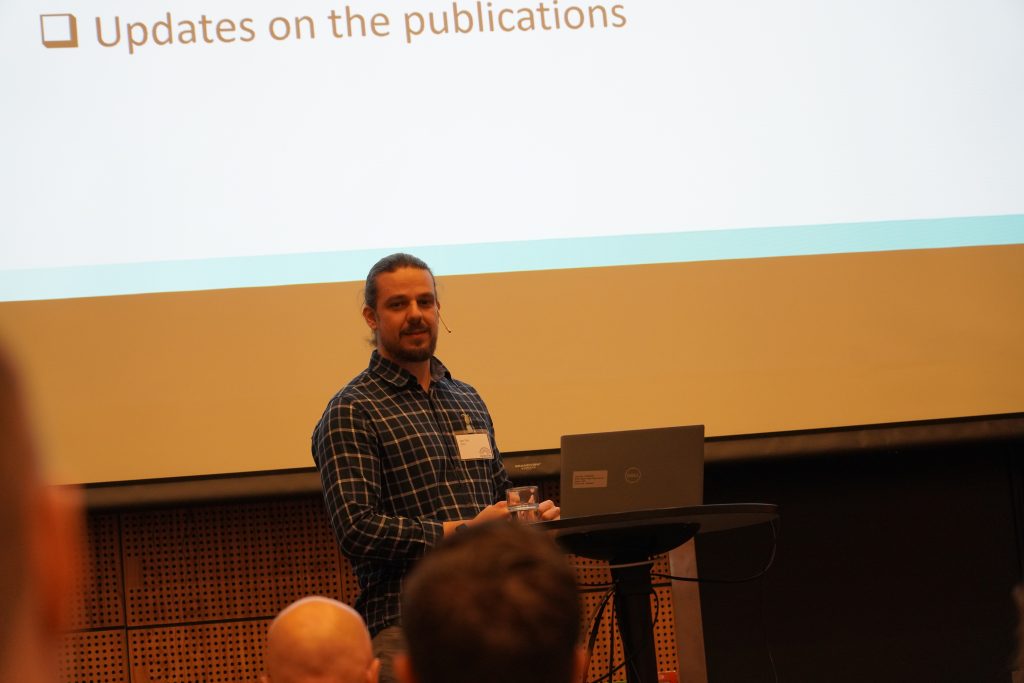
Igor Iliev, SINETF Energy As. Photo: Nirmal Acharya
In his talk, work package leader Igor Iliev summarized the research goals and results for WP3, Flexibility of turbines. The main objectives is to combine theoretical analysis, empirical data, numerical analysis and measurements to develop turbines that will handle future needs for flexibility. Specifically, the work package is organized around 4 main tasks
1. Development of design tools
2. Numerical analysis of flow fields and stresses
3. Validation through model testing
4. Development of turbine lifetime estimator
Within the project a complete tool chain for computer aided engineering (CAE) has been developed. This includes parametric design tool for Francis turbine runners and guide vanes, coupled with 3D CAD meshing and CFD and FEM analysis [1]. The tools permit both static and dynamic calculation and the results can automatically be coupled back to the design in a multi-objective optimization. To validate the tool the project has developed a new turbine runner to fit within the Francis 99 stationary components. The model runner has a modular design that will permit replacing the blade to perform testing on different blade geometries. The runner is equipped with strain gauges and pressure sensors. Logging equipment is installed in the hub of the runner, permitting data acquisition at all operating points. One challenge limiting the operating range of Francis turbines is the formation the so-called rotating vortex rope (RVR), that potentially can give rise to large pressure and power fluctuations. One activity within WP3 was to design and perform computations of a guide vane system in the draft tube. The computational results [2],[3] are very encouraging. The main challenge with flexible operation of Francis turbines is increased dynamic stresses that can impact useful operating time for the turbine. In order to estimate the impact of fluctuating stresses on the turbine life, Rainpower have developed a lifetime estimator as part of work package 3. Based on experimental fatigue data from typical material used in Francis turbines, the tool can include computational or experimental stress history assess the impact on residual useful life.
Video from workshop_Increasing Flexibility of Francis Turbines_Igor Iliev
Converter controlled synchronous machines, overcoming challenges in generators to switches (WP4)
Professor Urban Lundin, work package leader for WP4 started with addressing the rhetorical question “What does a flexible generator mean? His answer was “A highly efficient generator with a full power converter that can support the electrical grid”.
The specific topics addressed in WP4 related to the flexible generator are:
• Simulation of and control algorithms for a fully converted, variable speed unit
• Design and configuration for high voltage, large capacity converters
• Generator design and insulation aspects when operating with a full converter
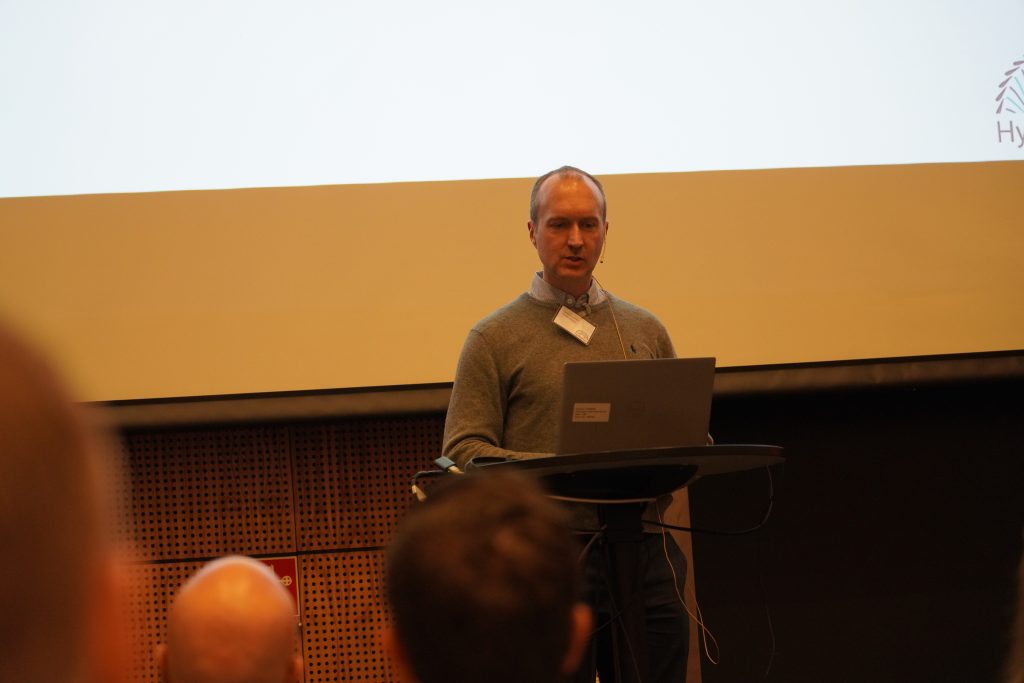
Urban Lundin, Uppsala University. Photo: Nirmal Acharya
With respect to control algorithms the team have developed a simulation model for a traditional high head power plant equipped with a full converter variable speed unit. By simulating a grid fault, causing a rapid frequency change, the variable speed unit shows superior behaviour compared to a traditional synchronous machine. The team have also investigated the behaviour of a fully converted motor-generator for a reversible pump turbine. The simulation shows that the fully converted solution substantially reduces the time it takes to switch from pump operation to turbine operation. The work package has also addressed details in the design of the frequency converter [4]. Various multilevel topologies were investigated in simulation model. The results show that by increasing the number of levels, the total losses (combination of conduction- and switching losses) in the converter can be significantly reduced in comparison with a two-level converter. One advantage of the fully converted solution is the possibility of installing converters in an existing hydropower plant. This can potentially increase the flexibility of existing hydropower plants. One potential downside and open question has been the impact of high frequency ripples due to the discrete approximate sinusoidal output from the converter. The high frequency disturbances may potentially cause a higher electric field or heat generation in the insulation, leading to increased degradation and premature failure of the stator windings. In this context the end winding is particularly vulnerable. Field grading is the technology used to smooth out the electrical and thermal load near the termination. The field grading is based on a combination of geometric parameters as well as capacitive and resistive properties of the insulation system. A finite element model has been developed and validated by laboratory experiments. The preliminary results highlight that there is a trade off between thermal and electric load and further work is required to optimize the termination suitable for high frequencies. Traditionally synchronous generators are equipped with damper windings on the rotor poles. Pole design with damper windings have multiple advantages including suppressing hunting and increase transient stability. Hower, these windings incur extra losses. Developing a generator design without damper windings may potentially increase the efficiency. However, this requires novel rotor and magnetization control maintain the positive properties of the damper winding. The concept has so far been tested in simulations and a ned model is under construction. Its completion is delayed due to supply chain issues, but the initial results are expected to be available before the end of the project period.
Mitigation of environmental impact from flexible hydropower (WP5)
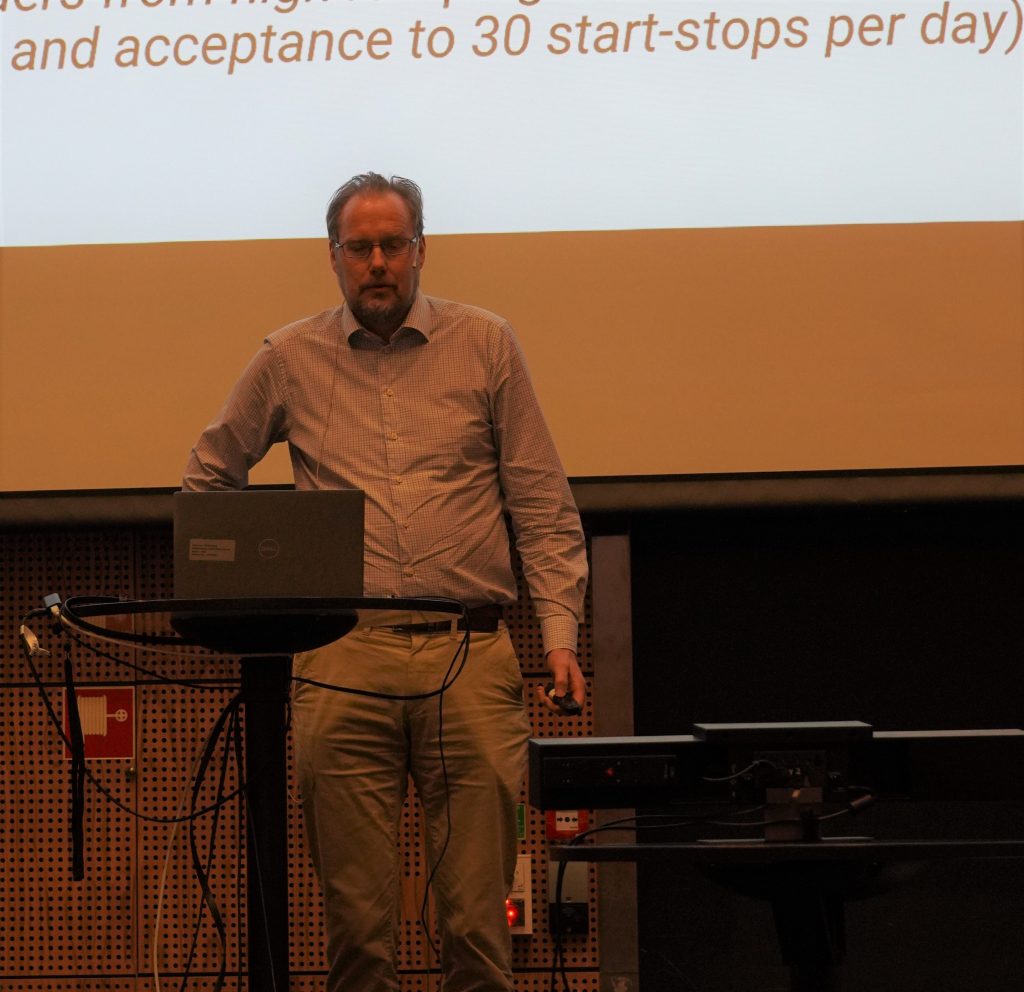
Staffan Lundström, Luleå University of Technology. Photo: Nirmal Acharya
Highly flexible hydropower plants can provide many important services to the power system. However, frequent starts and stops and large ramping rates may have detrimental impact on the surrounding environment as the water level downstream of the power plant may be significantly impacted by the variation in discharge. In his presentation, Professor Staffan Lundström, leader of WP5 presented the work to understand and mitigate the environmental impact from flexible hydropower. Two key tasks in the package are related to flow scenario modelling and fish population modelling. In their work, the team have focused on two rivers, Nidelva in the middle of Norway and Ume river in the Northern part of Sweden. Both rivers have substantial hydropower development. The hydrological model is used to determine how flow variation changes the flooded and dewatered regions in the river over time. Different time series are simulated based on different number of starts and stops and ramping rates. The distributed hydrological data was next coupled with a fish population model, permitting to model the stranding mortality. The individual based model IB Salmon was used to investigate the relation between flexible hydropower and the complete life cycle of the salmon. As part of the project a new agent based model for salmon has also been developed and is currently undergoing testing. Some of the main conclusions from the shows that in both rivers the changes in operating pattern impacts potential spawning area and thus may have impact on the fish population. However the impact in Nidelva was much stronger as the water level in the river was more directly impacted by the operation of the hydropower plant. For Ume, the discharge of Stornorrfors HPP is directly to the sea, so the water level is also strongly impacted by the natural tidal cycle in the Bothnian bay. One novel idea investigated in the project is to use an artificial, underground cavern to permit rapid ramping rates while simultaneously limiting the discharge variations. A numerical model for the concept denoted – Air Cushion Underground Reservoir (ACUR) has been developed. The simulations show that ACUR can decouple the discharge variations in the plant and downstream of the plant. Furthermore, the simulation indicate that the technology is better suited for a high head plant, like Bratsberg on the Nidelva river than for a low head plant such as the Stornorrfors HPP on Ume river. So far there has not been developed any cost model for the concept.
Video from workshop_Mitigation of environmental impact from flexible hydropower_Staffan Lundström
To flex or not to flex? – that is the question (WP6)
A frequently recurrent question in the hydropower community is the cost of operating the power plants more flexible. Overall, this includes both the material cost
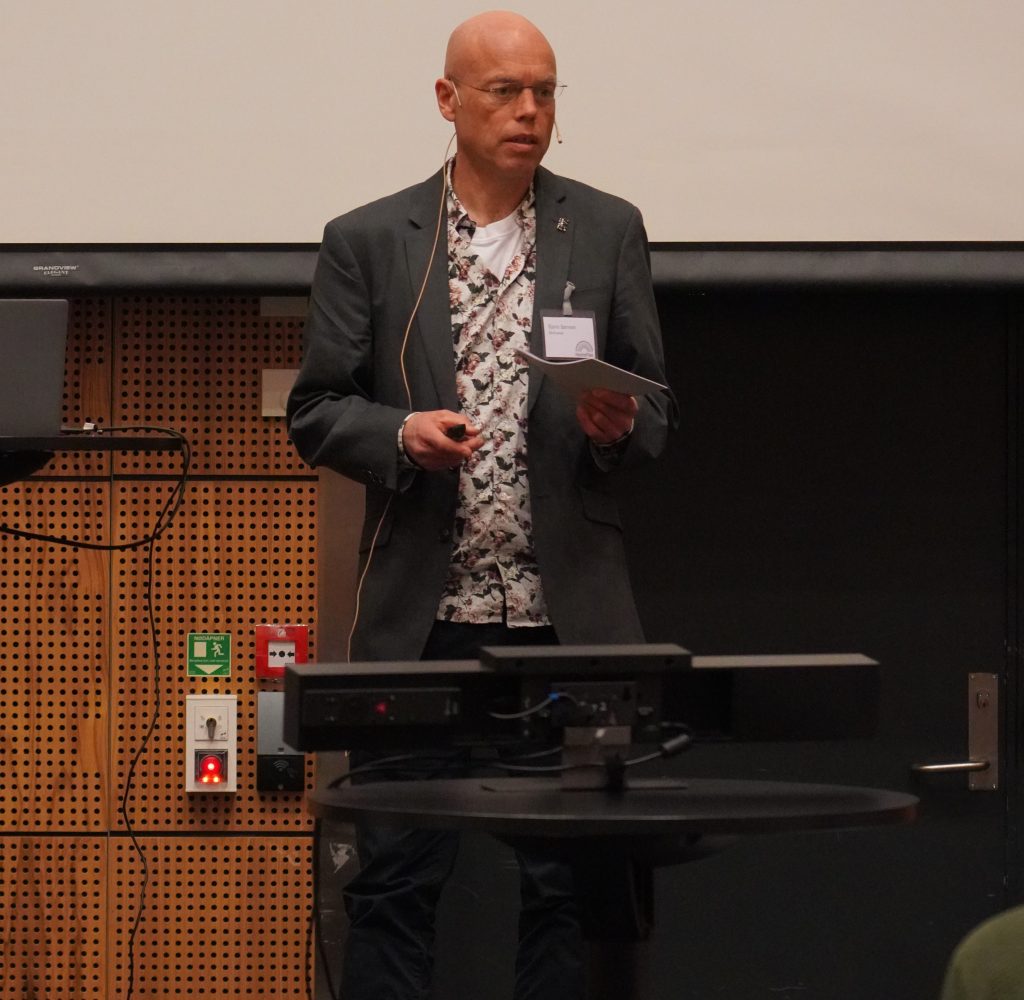
Bjarne Børressen, Multiconsult. Photo: Nirmal Acharya
due to increased wear and tear as well as reputational cost due to environmental impact and deterioration of social acceptance of the hydropower plants. In his presentation Bjarne Børresen, work package leader for WP 6, gave the status for development of the HydroFlex Tool. Focusing on the material cost a simplified
model to relative cost due to different operating pattern has been developed. The model is based on an analogy to the Palmgren-Miner rule used in fatigue analysis to account for various operating patterns. For a given operation, the degradation function will destroy a certain fraction of the useful life over a given time period. The model is calibrated by predicating a certain useful life for a baseline operating pattern. Next, more flexible operating pattern can be introduced. The reduction in useful life can be expressed as a relative increase in the operational expenses.
Video from workshop_To flex or not to flex? – that is the question_Bjarne Børressen
Panel debate
As part of the closing of the workshop a short panel debate with all work package leaders, industry representative from Vattenfall and the head of the Norwegian research centre HydroCen was conducted. From the industry perspective it was commented that they were impressed with what had been achieved in laboratory scale so far in the project. However, to really confirm the findings large scale demonstrators should be the next step. Liv Randi Hultgren, leader for HydroCen reflected on the duration of the project and how quickly the energy situation and scenarios has changes just in the recent time, and to which extent the project is able to adjust to the changing surroundings. Professor Ole Gunnar Dahlhaug underlined the importance of commercial viability of flexible hydro in order support and ensure future development. The industry actors need to see solid business cases in order to invest in projects that may take a long time to develop.
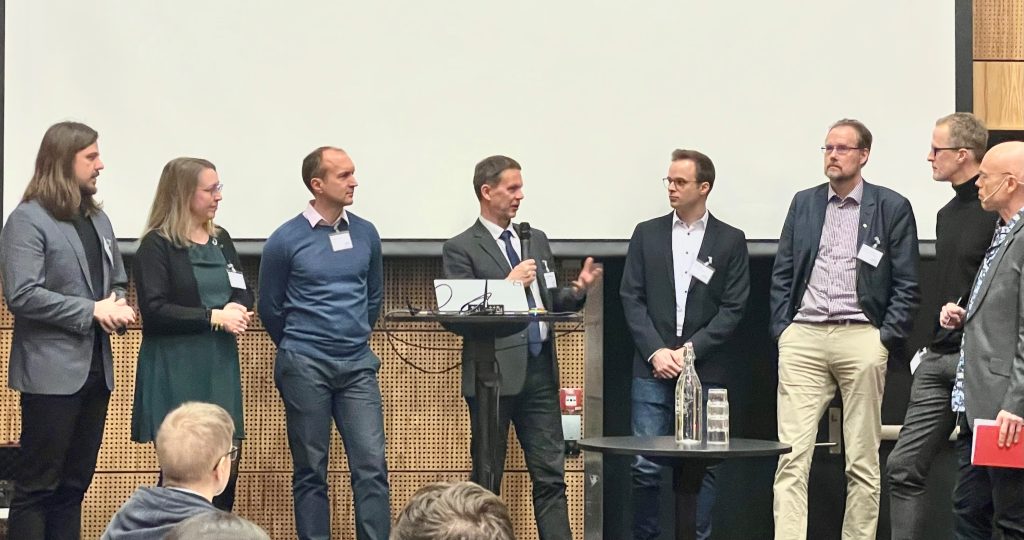
Panel Discussion. Photo: Shreejana Poudyal. From Left: Igor Iliev (SINTEF), Liv Randi Hultgreen (HydroCen), Urban Lundin (UU), Ole Gunnar Dahlhaug (NTNU), Peter Wirtz (RWTH Aachen), Staffan Lundström (LTU), Mats Billstein (Vattenfall), Bjarne Børressen (Multiconsult)
The panel was also challenged to reflect on what they expect to be the lasting results from the project in the coming decade. From the market side it was again observed that the flexibility requirement is more driven by development of variable renewable energy within the Nordic region, rather than the development in the continental European grid. From the turbine side it was observed that wide operating range will become even more important compared to the peak value at the best efficiency point. From his point of view Urban Lundin sketched out a scenario of more diversification of the installed fleet. Not all generators will be equipped with frequency converters but having some units in a plant that are more flexible, either with full converter or other systems, and others that are work horses tailored more for energy production will give more flexible and robust power system overall. In the discussion it was also highlighted that there are different driving forces at play at the moment. Increase share of variable renewable energy requires more storage and flexible units to balance the system when there is either no wind or too much wind. At the same time, the water framework directive and other environmental regulations is constraining operation and regulation and can potentially lead to less flexibility. Staffan Lundström stated his conviction that the results from the project can be important tools and method used to optimize operation and ensure a good trade-off between environmental requirements and the need for flexibility in the power system. He also briefly reflected on the importance of the Nordic collaboration, and both the Swedish and Norwegian research communities have benefitted both from friendly competition and collaboration.
Video from workshop_Panel discussion
Closing remarks
In his closing remarks, Sebastien Mortier EU project officer congratulated the project with the completion of the public workshop. Through the results and the communication, both within this project as well as other initiatives, the importance of hydropower is becoming clearer and better understood in EU and in Brussels. He underlined the important to acknowledge and address the concerns regarding environmental impact and public acceptance for hydropower to properly fulfil its role. Even though there will always be room for improvements, in general the completion of the project and results obtained are highly satisfactorily.
Professor Ole Gunnar Dahlhaug as project coordinator closed off the final workshop and reflected on the fruitful collaboration between all the project partners. “Based on my experience from the HydroFlex project I do not have any worries for taking the role as coordinator in a possible future project” he stated.
Video from workshop_Closing remarks_Project Officer Sebastien Mortier
Video from workshop_Closing remarks_Project Coordinator_Ole Gunnar Dahlhaug
References
1 HydroFlex deliverable 3.6 Parametric Design Tool, April, 2022
2 HydroFlex deliverable 3.2 Guide vane system in the draft tube, April 2021
3 Jesline Joy, Mitigation of Pressure Pulsations in Francis Turbine Draft Tube with a Guide Vane System: A Numerical Investigation, Licentiate Thesis, June 2021
4 Chengjun Tang and Torbjörn Thiringer, Performance comparison of five-level NPC and ANPC converters in medium voltage drives for hydro power application, 23rd European Conference on Power Electronics and Applications (EPE’21 ECCE Europe), 2021
Leave A Comment